Designing and building a bifacial PV power plant is not much more difficult than building a monofacial power plant. Optimizing a bifacial solar plant, however, is far more complex. Bifacial energy gains are sensitive to many variables that do not impact monofacial plants, such as tracker height-to-width ratio and obstructions below the module, to name a few. Of course, albedo is the most critical parameter that uniquely impacts additional bifacial energy yields. These factors explain why there will always be some differences in bifacial gain across sites.As an enterprise with more than ten years of experience in the design and manufacture of solar mounting systems, CHIKO Solar has something to say.
Techren 2 solar farm in the Nevada desert, featuring NX Horizon trackers paired with bifacial technology. Photo credit: Swinerton Renewable Energy
1. Ground Reflectance: The Ever-Changing Albedo
Albedo is a dimensionless quality that describes the ratio or percentage of surface-reflected light to the original incident irradiance. Part of the challenge of accounting for ground surface reflectivity in bifacial applications is that albedo is not a single value. Not only does the magnitude of the albedo change based on the time of day or year, but also the spectrum of the albedo changes based on the ground cover. The spectrum of the albedo is different for grass versus rocks versus snow. Since it is impractical for developers to artificially increase albedo in free-field applications, the relevant project optimization goal is to accurately characterize site-specific average or monthly albedo values.
2. Back-Side Shading: Obstructions Impact Gains
Tracker solar mounting system design and orientation also have a significant impact on bifacial gains. These factors include:
Torque tube shape
Torque tube distance from the back of the module
Post and bearing orientation
Tracker height-to-width ratio
Row-to-row spacing
View factor
Obstructions located between the modules and the ground will impact bifacial gains. These obstructions can include balance-of-system components, such as wire trays, PV wire, combiner boxes, and so forth. The support structure itself also contributes to back-side shading. Unlike albedo, project design engineers can influence back-side shading via strategic product selection and design decisions.
3. Module Mismatch: The Relevancy of Irradiance Levels
In the field, strings of PV modules are wired in series so the same electrical current passes through each module. In a 1,500-volt system, 28-module strings are typical. Unfortunately, the optimal output current to achieve maximum output power may be slightly different for each PV module. The level of the optimal output current is influenced by multiple factors including manufacturing variations, degradation, and irradiance. Nonuniform degradation of mono- or bifacial PV modules can be caused by potential-induced degradation (PID), light and elevated temperature induced degradation (LeTID), encapsulant yellowing, and other factors.
For bifacial PV module technology, the relevant irradiance level for determining module mismatch is the combination of front-side and back-side irradiance. In the absence of shading from nearby objects, such as trees or adjacent module rows, the front-side irradiance level is typically consistent across modules. However, the irradiance on the rear side of the module is impacted by obstructions between the back of the module and the ground. Minimizing these obstructions will reduce mismatch losses.
4. Electrical Stringing: Potential Source of Mismatch
In 2P-tracker designs, electrical stringing is also a potential source of module mismatch. Specifically, it is suboptimal to have modules from an upper row in the same electrical string as modules on a lower row. In this scenario, the intensity of the reflected sunlight on the back side of the modules varies between the rows based on distance to the ground. This irradiance non-uniformity will increase mismatch effects. Similarly, portrait versus landscape orientation could have an impact on mismatch based on whether the nonuniform back-side irradiance is perpendicular to or in parallel with the cell strings and bypass diodes.
PV module selection is one of the most dynamic and critical aspects of developing a solar project. Module technology is evolving quickly in many ways:
Form factors and power ratings are increasing.
Many manufacturers are increasing wafer size; others are using half-cut or even third-cut cells.
Internal circuit wiring methods differ.
Bifacial modules may have glass-glass or glass-backsheet designs.
Bill-of-material (BOM) details will vary, based on manufacturer, factory, or even batch.
Bifacial modules can exhibit different degradation on the front and the back, which will impact bifacial energy gains over time.
Selecting the right product for a given project will always depend on site-specific environmental conditions as well as project-specific financing requirements. PVEL’s Product Qualification Programs (PQPs) are focused on evaluating the quality of PV modules, inverters, and energy-storage systems across a comprehensive set of reliability and performance tests. Developers and banks can access these PVEL reports at no cost to help with vendor selection.
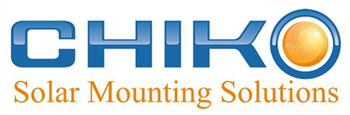
Above news from CHIKO Sales & Marketing department
Add: No 680 Xingwen Rd. Jiading dist. Shanghai 201801 China Email: Chiko@Chikolar.com
Website: http://www.chikolar.com Fax : +86 (21)59972938
Phone: +86(21) 59972267 59973712 59973713--811