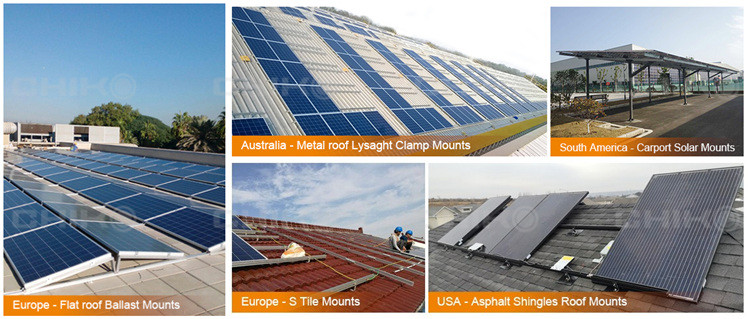
Connection method of Solar mounting system
Welding and assembling are the two main connection methods of solar brackets. Welding has lower requirements for angle steel, lower price, better connection effect, stronger and more common application. The problem with welding is that the connection points are prone to corrosion, and the maintenance cost will be higher. Anticorrosion work should be carried out every other year to avoid problems with the bracket. Because the maintenance work is more troublesome and the cost is higher, welding The cost is very high. In addition, when welding is used in field installations, it will consume a lot of power and also increase costs. Although the welding has lower material requirements and link effect numbers, the process is slightly rough, the bracket is not beautiful, and it is more and more incompatible with people's aesthetic needs. Therefore, the solar panel bracket has gradually become unsuitable for the use of welding brackets.
Channel steel is gradually replacing these welded brackets to overcome the above problems. As a kind of splicing bracket, the channel steel finished bracket does not need to be welded on site, but can be spliced directly on the spot by the bolt. The installation speed is fast, beautiful, very durable, easy to adjust. , Firm and easy to disassemble.
All bracket products of CHIKO Solar adopt AL6005 grades, processed in T5 state, and the surface is anodized 12-15MIC; all stainless steel materials are 304 grades; steels are Q235 grades, and the surface treatment is hot-dip galvanized with an average of 80MIC. After a high degree of pre-assembly, there is no need for on-site cutting and welding, saving time and labor costs.
Connection of Solar mounting system base
The form of the double-row column type bracket depends on the actual situation. In general, the roof solar construction can adopt the method of concrete block counterweight and embedded parts, and the construction of solar power station adopts the ground paving method and the direct buried type. Different methods are applied to different aspects, and they will receive different effects. The first two methods are mainly to prevent the roof waterproof layer structure from being damaged, and the latter two are applied to the entire power station to improve the safety and reliability of the power station and thus operate normally.
In the construction of solar power stations, the safety factor of the ground anchor method is very high, which is a commonly used method during construction. However, the ground anchor method pays a high cost, and is carefully designed and customized to make the connection point of the solar bracket stronger. The direct-buried method is simpler than the ground anchor method and does not need to be customized. However, before conducting the direct-buried method, a geographic survey experiment should be conducted to ensure that the low-quality is very direct-buried. The Solar mounting system is more suitable for the direct burying method, because its arrangement is restricted by the solar panel.
Installation of new cold-bent thin-walled solar mounting accessories
1) Connection of steel structure members. The material of the new cold-bent thin-walled solar bracket is mainly made of a variety of mixed steel and plastics. Generally, it is necessary to book and make in advance. Because these steels and plastics are diverse, they are widely used as long as they meet the installation requirements. Conditions are sufficient. Ensuring the correct connection of the steel structure components is the prerequisite for the design of the support structure.
2) The bracket is connected to the foundation. The connection method of the new cold-bent thin-walled solar bracket and the foundation is generally independent, but in poor conditions, it is best to use a strip foundation and other foundations that can adapt to poor geology and poor
3) Bracket purlin connection, there are three ways of bracket purlin connection: rigid connection, hinged connection, semi-rigid connection, and hinged connection is the most convenient. When encountering harsh environments such as strong winds, the beams and columns of the support should be rigidly connected by rigid connection. The semi-rigid joint has the performance that the hinge does not have, and it also makes up for the complicated construction of the rigid joint, which has the advantage of making up the shortcoming of the two. However, semi-rigid joints are generally not used during construction.
Technical difficulties of solar mounting system
The solar panel bracket has very high requirements on the process. From the perspective of materials, if the section steel is to improve quality, it should be manufactured by a skilled galvanizing process and meet the relevant national standards. Due to the extremely high requirements of the galvanizing process, the thickness of the galvanized layer to the ease of manufacture should be strictly implemented in accordance with the standards. If it does not comply with the regulations, it may cause problems in use, such as corrosion. Among them, halogen has the greatest impact on steel corrosion, and its rapid corrosion rate and wide range will quickly cause the stent to be weak and cause serious quality problems. It can be seen that the premise of manufacturing a high-standard solar bracket is to have a higher level of galvanizing process.
From the connection point of view, the connection method of section steel also needs to be cleverly conceived and continuously developed. Many people have conducted many years of research on this, and have formed a set of proven connection methods that belong to the section steel. In the connection, not only the safety of the connection parts, but also the design of all aspects of the channel steel, such as saving steel, easy installation, cost reduction, and fast adjustment, must be considered. In short, the connection method of section steel needs to be continuously excavated in order to keep up with the rapid scientific development.
From the application point of view, if it is double-sided channel steel, it must have a great bearing capacity, so back-to-back welding is used. The use of pressure laser welding and electric welding will have completely different effects. The former can achieve the purpose of back-to-back welding, and the double-sided channel steel can be combined into one, uniformly connected and beautiful; while the latter can achieve channel steel connection, but it cannot be completely The connection can also be done with a square tube.
CHIKO focus on manufacturing and design Solar Mounting System for more than 10 years, CHIKO products was installed in more than 60 countries.The customer design is available.
Anything further question and more solution, Contact us !
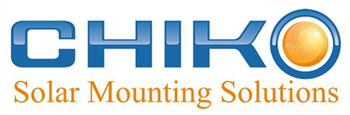
Above news from CHIKO Sales & Marketing department
Add: No 680 Xingwen Rd. Jiading dist. Shanghai 201801 China Email: Chiko@Chikolar.com
Website: http://www.chikolar.com Fax : +86 (21)59972938
Phone: +86(21) 59972267 59973712 59973713--811